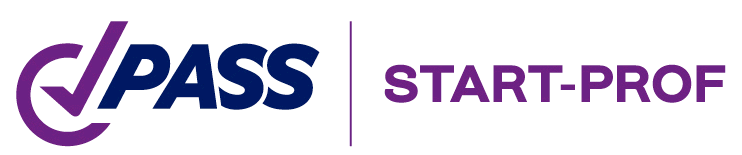
How to Reduce the Nozzle Loads in
START-PROF
Read
about START-PROF pipe stress analysis software
If the equipment load is greater
than the allowable values as specified above, first try to understand
the reason of the increased load. The increased load may be caused by:
- Force-controlled
loads: Weight loads, Pressure thrust forces, etc. Can
be obtained if operating temperature is equal to ambient temperature.
Weight multiplier should be 1.0
- Displacement-controlled
loads: Thermal expansion, Support displacement, etc.
Can be obtained if weight multiplier in operation
mode editor is zero.
If high loads are caused by
force-controlled loads then:
- If the load is due to
the weight of the piping system, provide additional vertical supports,
variable spring hangers and supports
- If the load is due to
the expansion joint thrust forces then piping design is wrong, remove
the not pressure balanced expansion joints from the model or add anchors
to resist the thrust forces
If high loads are caused by
thermal expansions then try to apply any of the following methods to reduce
the nozzle loads:
- Try to reduce the nozzle
load by adding flexibility to the piping system
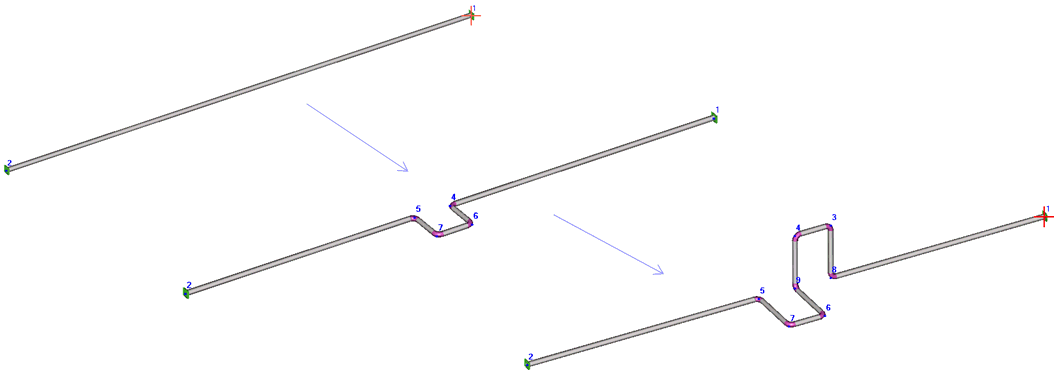
- Add more bends as bends are more
flexible than the straight pipe
- Reduce the pipe and bend
wall thickness if possible. The more thin pipe you use, the more flexible
piping system you have
- Reduce the diameter if
possible. The smaller diameter you use, the more flexible piping system
you have
- Add the nozzle
flexibility using WRC 297/PD 5500, API 650 or Nozzle
FEM
- Add the pipe support
and support structure flexibility using custom
restraint with flexibilities
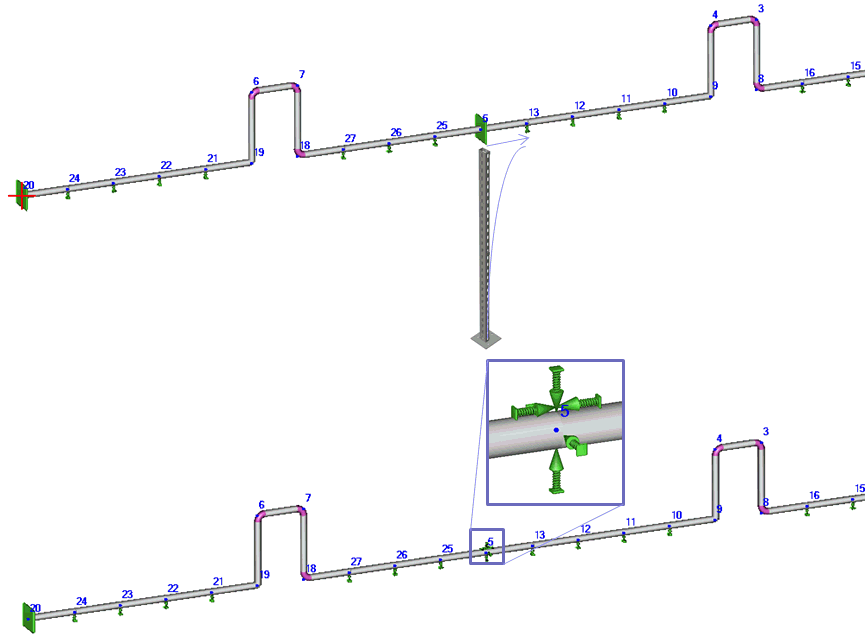
Let's show it on the simple
example of the straight pipe between two anchors.
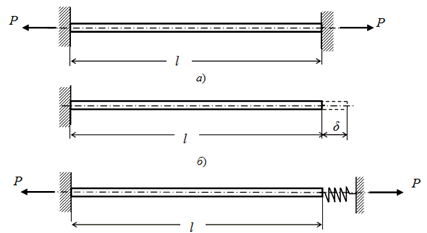
Without considering the anchor
flexibility the axial force must be calculated by the equation:

If we consider right nozzle
flexibility λ, then the equation is

For example, pipe 219x6 mm,
l= 6m, dT=100 degrees, α=0.000012, E=2000000 kg/cm2, A=40.1 cm2 we have
kgf
if we consider the nozzle
flexibility λ=0.14 mm/tf (very stiff nozzle) then the nozzle load reduces
for 3 times!
kgf
Here are
the complete equations to determine support loads, internal forces, stresses
for restrained, unrestrained, and restrained pipe with flexibility
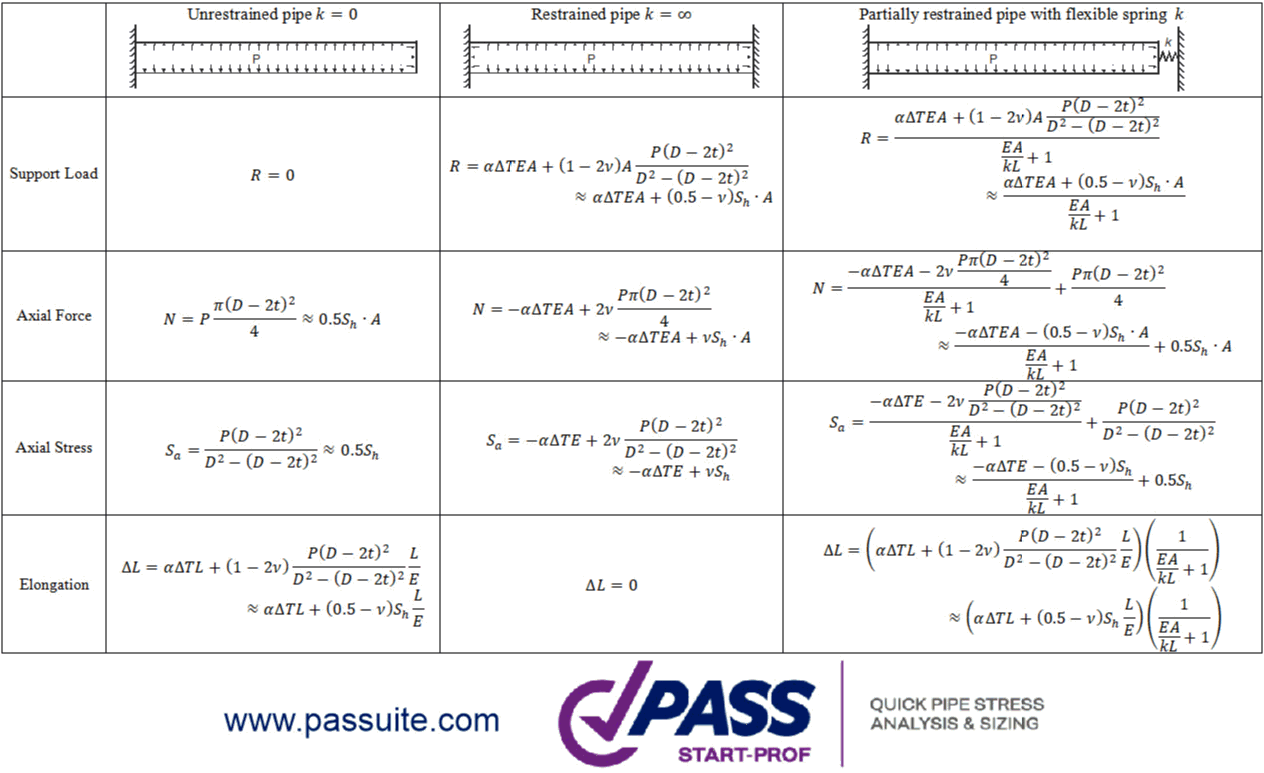
Using of the unbalanced expansion joints should be careful. The thrust
force may transfer the huge axial load on the equipment
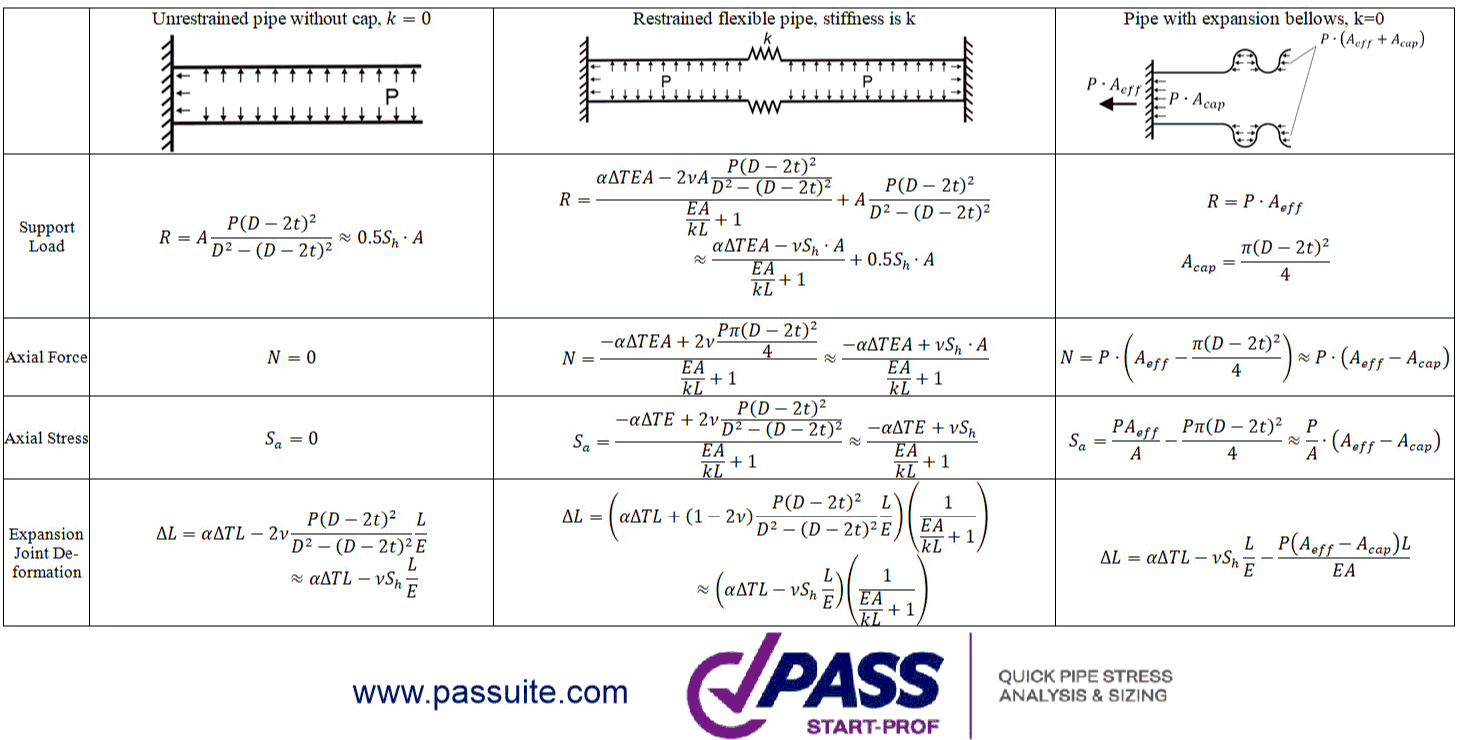
Here are the possible correct and wrong variants of pump piping with
unbalanced expansion joint
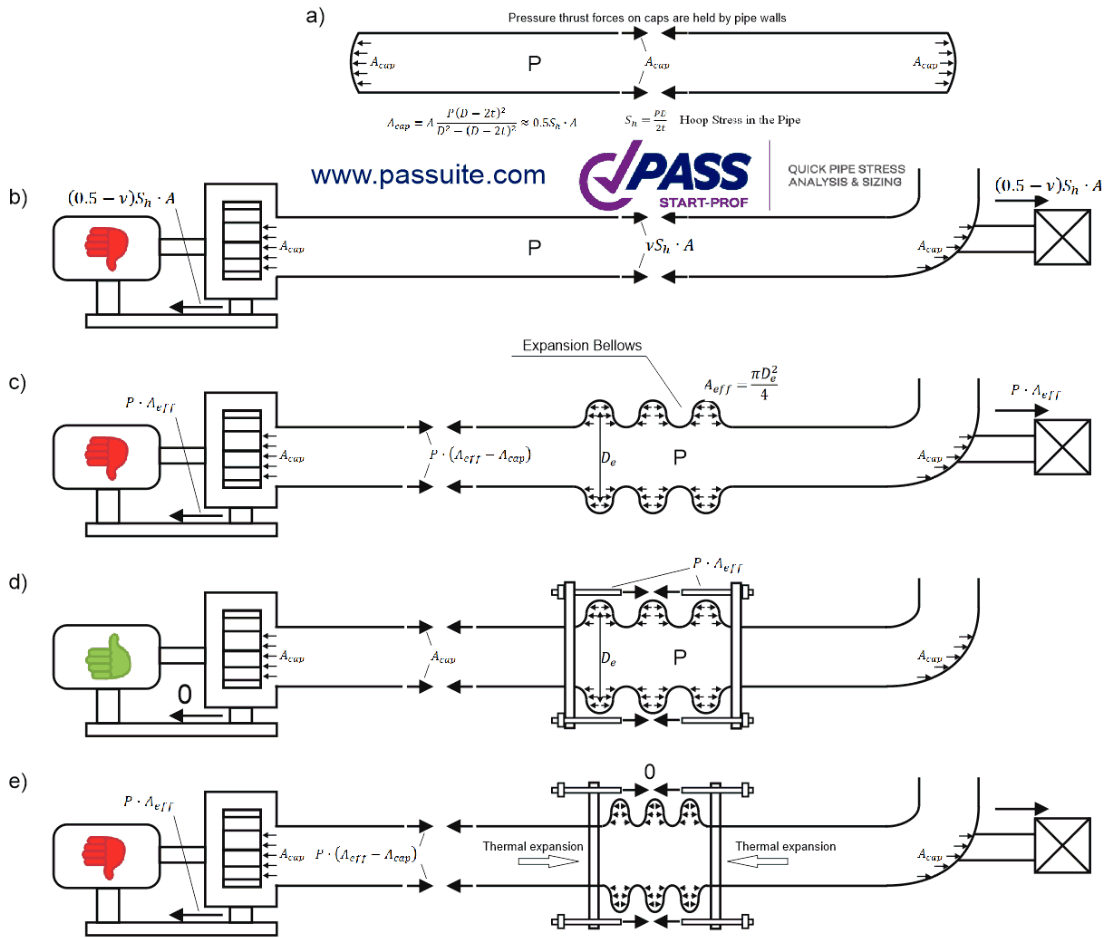
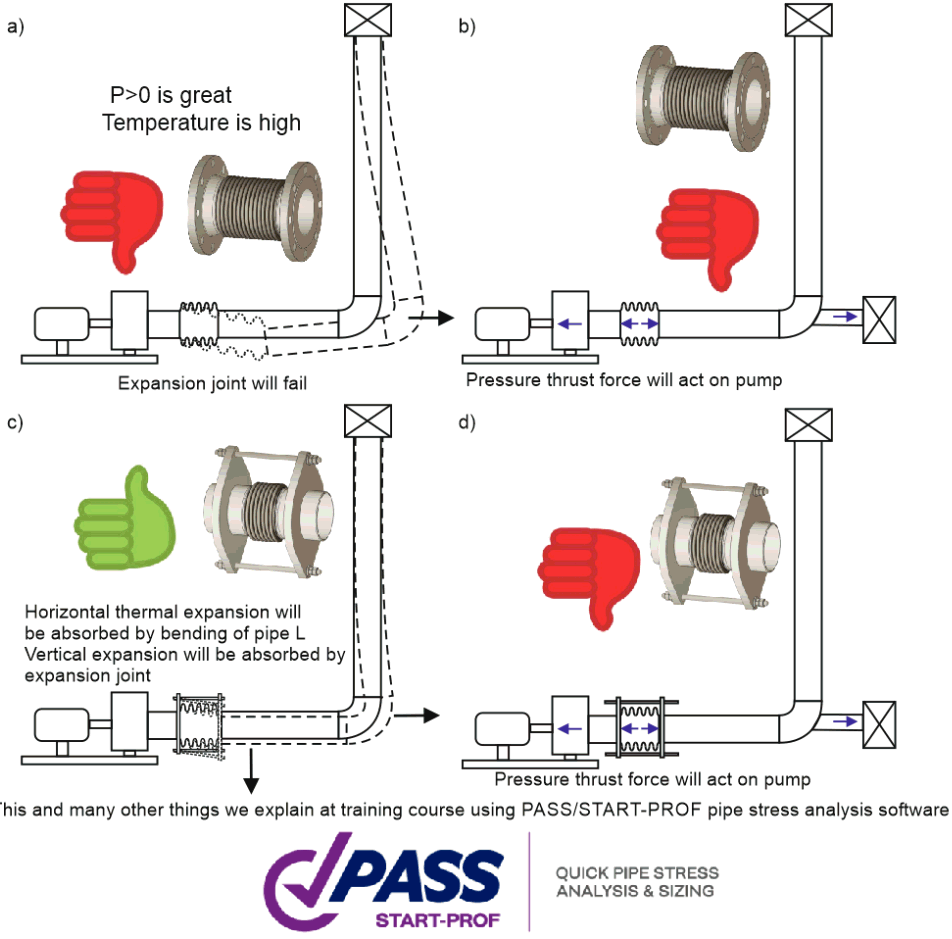
- Reduce the temperature
difference. Reduce the operation temperature or raise the Ambient
temperature. Remove unnecessary reserve
- Try to direct the
thermal expansion away from the equipment (for example to the U-shaped
loop) by providing proper restraints (guide or directional anchors).
Also don't forget about the huge friction
forces in such anchors, that may raise the big axial force in
1-2 pipe.
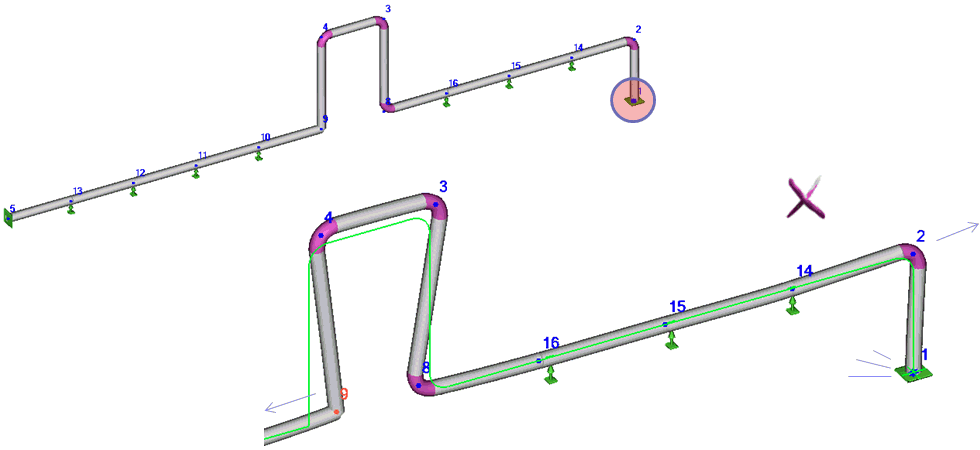
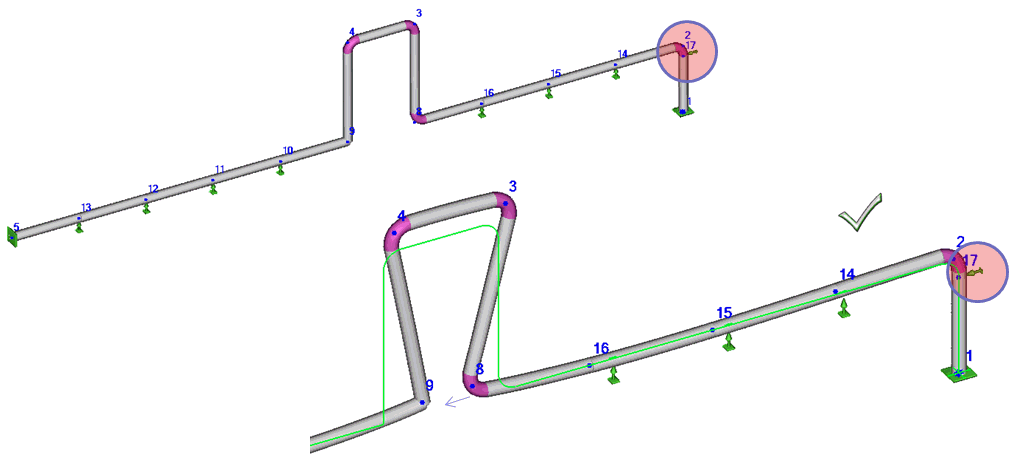
- If the load is
high because of friction
then try to use Teflon/graphite/polished stainless steel plates to
reduce friction forces
- Hot modulus of
elasticity can be used to calculate equipment nozzle loads (option
"Use Eh for support loads" in Project
Settings)
- Cold
spring can be applied if no other way. But note, that cold spring
don't reduce the expansion stress range
- Move the equipment to
the half of the piping thermal expansion value from installation to
operating mode
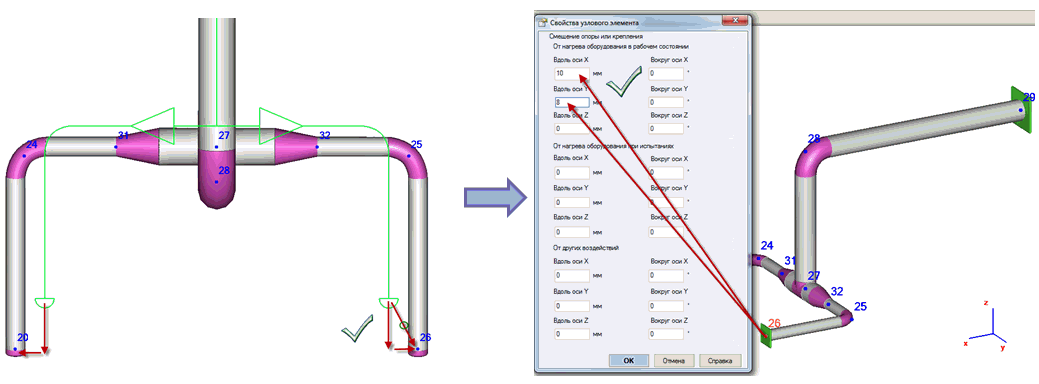
Even after all trial and error if it is not possible to reduce the loads
within allowable limits then forward the actual load values (increased
by at least 20% if all piping data is not final) to vendor for FEA analysis
and their acceptance.