Version |
Update list in 3.5 |
3.5 20.03.2024 |
- The ability has been implemented to add multiple nozzles or structure attachments.
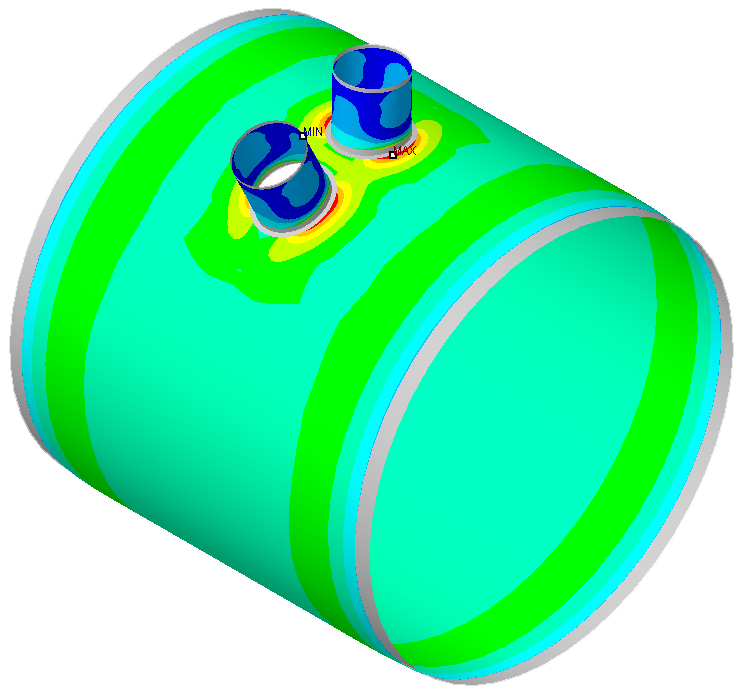
- The ability has been added to preview the model with loads and boundary conditions,
as well as launch the post-processor from the user interface (UI).
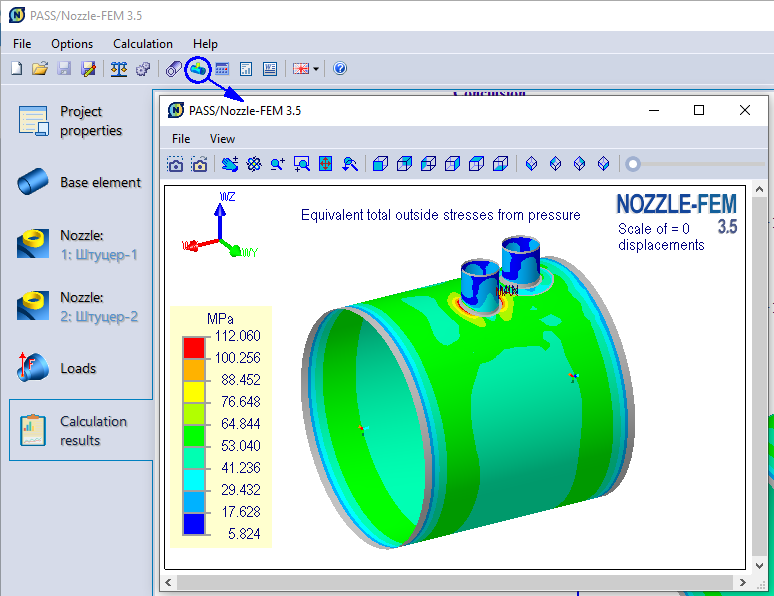
- The new separate types "Plate" and "Two plates" of the structure attachment have been added.
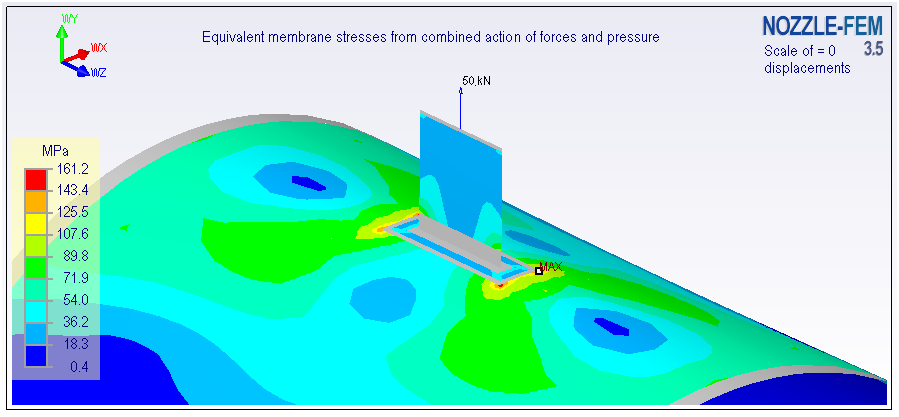
- The mutual influence of openings has been added when calculating as per GOST 34233.3-2017.
- The stress analysis has been updated for ASME BPVC.VIII.1-2021.
- The stress analysis has been updated for ASME BPVC.VIII.2-2021.
- The stress analysis has been updated for EN 13445-3:2021.
- The new program protection system has been added (Guardant Sign keys, Web licenses).
- The program manual was updated.
|
3.5.1 07.07.2024 |
- The errors of the program protection system and updating have been fixed.
- The calculation of the stress intensification factors (SIF) of the base element with nozzle crotch has been corrected.
- The errors of the geometric model creation and the finite-element mesh generation have been corrected.
|
3.5.2 16.08.2024 |
- The accounting of the support locations at the ends of a conical reducer has been added when importing from the PASS/EQUIP program.
- The import of weld sizes from PASS/EQUIP program has been fixed when ASME standard document is specified.
- The creation of geometric model with zero weld size on nozzle has been fixed.
- The creation of geometric model of axial nozzle junction on conical surface has been fixed when D1 < D2.
- The calculation of conical element according to i. 8.3.6 of GOST 34233.2-2017 has been fixed.
- The boundary conditions for a flat head without a cylindrical part have been corrected.
- The errors in working with licenses from the Welcome window have been fixed.
- The errors of finite-element mesh generation were fixed.
|
3.5.3 30.08.2024 |
- The skirt support import from PASS/EQUIP has been fixed.
- The errors of UI data when creation of skirt support and bend stanchion have been fixed.
- The errors of finite-element mesh generation were fixed.
|
3.5.4 05.12.2024 |
- The errors in interaction with PASS/START-PROF have been fixed.
- The import errors from PASS/EQUIP have been fixed.
- The calculation errors of stress intensification factors have been corrected, in particular, for bends with large radii.
- The errors in modeling shell sections of the nozzle inner part for tank junctions have been fixed.
- The modeling errors of multiple attachments to the tank base element have been fixed.
- The errors of the program protection system and updating have been fixed.
- The errors of the geometric model creation and the finite-element mesh generation have been corrected.
|
3.5.5 25.01.2025 |
- The hydrostatic pressure import has been added from PASS/START-PROF.
- The nozzle junction of air cooler has been added from PASS/EQUIP.
- The setting of fatigue strength reduction factors (FSRF) has been fixed for models with multiple attachments.
- The geometric model with nozzle crotch of big radius (sweepolets, etc) has been corrected.
- The geometric model of rectangular plate has been corrected - the thickness of the side wall was taken into account.
- The errors in report generation have been fixed, including for correct operation under Wine (Linux).
- The errors of the geometric model creation and the finite-element mesh generation have been corrected.
|
3.5.6 12.05.2025 |
- The setting of the fatigue curve setup (UI) with user parameters has been fixed when performing the fatigue analysis to ASME BPVC.VIII.2.
- The pressure applying on the nozzle internal part has been corrected.
- The allowable stresses calculation of materials according to EN 13445-3 has been fixed for which information on elongation after fracture was missing in the database.
- The translation of report generation templates in Chinese has been fixed.
- The errors of the geometric model creation and the finite-element mesh generation have been corrected.
|
Version |
Update list in 3.4 |
3.4.0 12.12.2022 |
- The structure attachment (I\H-beam, channel, and other sections) was added.
- The bend stanchion with structure section was added.
The user interface for bend stanchion was changed to unify with the attachment UI.
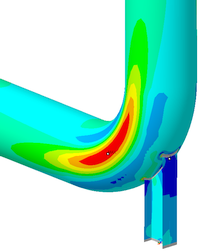
- The axial nozzle for a conical head was added.
The axial nozzle insertion on a conical head from the "Head" UI-branch is now carried out on a flat part,
and the insertion from the UI-branch "Conical shell" is made on the conical part.
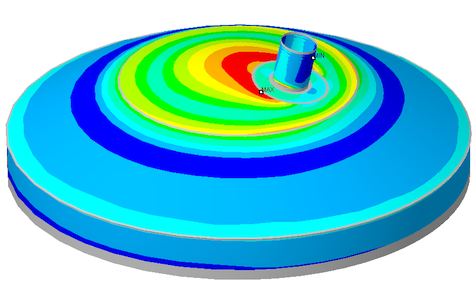
- The ability to set the global axes orientation (select the vertical axis, etc.) was added.
- The ability to set the weld size on the edge of the flat head was added.
- The average radius calculation of the design shell model was changed.
Since version 3.4, the average radius is calculated taking into account corrosion,
which can lead to a slight increase stresses from internal overpressure.
This change was made in order to get the same results when the user enters a corrosion allowance, and when he subtracted it from the thickness himself.
- The ability to specify the weld size on the attachment (nozzle) edge was added.
- The option "Disable corrosion" for the load case under testing conditions was added.
- The orientation nozzle with "Offset" placement type for conical shells to be compatible with PASS/EQUIP was changed.
The offset nozzle must be in the plane of the cross section of the base element now.
- The new finite element mesh generator was embedded.
- Two separate categories of floating point formats were added for the user interface and reports.
- The floating point number formats for different value categories (dimensions, stresses, stiffness, etc.) used in report generation were added.
- Spanish language was added to the program (user interface, reports, user manual).
- The error in the strength factors output when stress analysis calculating in accordance with GOST 34233.1-2017 was fixed.
- The error of output of the allowable number of cycles for GOST 34233.6-2017 (fatigue damage calculation) was fixed.
- The calculation of opening reinforcement as per GOST 34233.3-2017 for conical shell was corrected.
The design radius in the junction region was clarified.
- The average radius calculation of the hemispherical head curvature in the junction region according to GOST 34233.3-2017 was corrected.
- The membrane stresses checking by allowable total membrane stresses (WRC 537/297) was corrected.
- The calculation according to WRC 537/297 was corrected, taking into account the design, operating conditions for one load case.
- The import from XML-file of PASS/EQUIP was fixed.
- The boundary conditions for the operating mode, taking into account thermal strains were corrected.
- The error of launching the material database dialog in Chinese was fixed.
- The error of flexibility factor calculation of the bend from torque was fixed.
- The RTF templates were fixed.
- The program manual was updated.
|
3.4.1 07.02.2023 |
- The errors of finite-element mesh generation were fixed.
- The report generation error for model without an attachment was fixed.
- The model creating of rectangular plate (wall) with a structure attachment was corrected.
- The duplication of design and operating load values in user interface for JB4732 was fixed.
- The definition of the inner diameter of a cylindrical shell in GOST 34233.3 was corrected
for cases where the nozzle diameter coincides with the base element diameter.
|
3.4.2 07.03.2023 |
- The geometric model of nozzle junction with crotch was improved.
- The report generation errors for the structure attachment were fixed.
- The allowable loads definition was corrected in accordance with
the status of the option to enable\disable the checking of general membrane stresses.
- The export (allowable loads, SIF, flexibilities) to PASS/START-PROF program for several load cases was fixed.
- The language switching of user interface was fixed when PASS/NOZZLE-FEM is called from PASS/START-PROF.
- The errors of finite-element mesh generation were fixed.
- The user interface errors were fixed.
|
3.4.3 23.05.2023 |
- The ability to set a code for calculating the flexibility factor, stress intensification factors was added.
- The support for long file paths (more than 260 characters) was added.
- The creation of a geometric model of an equal tee with specified thickness allowances was fixed.
- The construction of a geometric model with the elbow attachment was fixed when θ is zero.
- The check of insertion of the bend stanchion was fixed.
- The check of insertion of the structure attachment with the rectangle reinforcing was fixed.
- The check of material properties for mount conditions as per GOST 34233.1-2017 was fixed.
- The error in the output of the report for the calculation of conical heads as per GOST 34233.2-2017 was fixed.
- The error in the calculation of the nozzle with weld-in ring as per GOST 34233.3-2017 was fixed.
- The error of finite element mesh generation was fixed when working in Windows 7.
- The errors of finite-element mesh generation were fixed.
|
3.4.4 08.08.2023 |
- The geometric model creation of a spherical unbeaded head was fixed.
- Methods for calculating flexibility factors and stress intensification factors were refined,
taking into account various codes for calculating pipeline systems,
including the axial stress intensification factor for a bend (elbow).
- The determination of allowable stresses for ASME.VIII.1,2 by one yield strength was allowed
for temperatures at which creep and long strength do not occur.
- The robustness of building a finite element model was improved,
which reduces the volatility of the calculation results during repeated runs.
- The errors of finite-element mesh generation were fixed.
|
3.4.5 30.08.2023 |
- The errors of the report output for some Windows build versions were fixed.
- The geometric model creation of a head without attachments was fixed.
- The geometric model creation of a spherical unbeaded head with a nozzle was fixed.
- The output error of the calculations as per GOST 34233.2,3 for the test and installation conditions was fixed.
- The errors of finite-element mesh generation were fixed.
|
3.4.6 20.09.2023 |
- The error of the data importing from PASS/START-PROF was fixed.
- The error of an attachment junction creation on the plane surface was fixed.
- The errors of finite-element mesh generation were fixed.
|
3.4.7 07.11.2023 |
- The error of blocking some program functions when opening from a file manager has been fixed.
- The errors of finite-element mesh generation have been fixed.
|
3.4.8 05.02.2024 |
- The error of the string loading of the language localization has been fixed, that occurred when generating reports.
- The errors of finite-element mesh generation have been fixed.
|
Version |
Update list in 3.3 |
3.3.0 27.05.2021 |
- The fatigue assessment was added as per ASME BPVC.VIII.2-2019.
- The calculation control options were extended as per ASME BPVC.VIII.2-2019 and EN 13445-3.
- The capability to set design and operating loads was added as per ASME BPVC.VIII.2-2019 and EN 13445-3.
- The capability to set cyclic loading and corrosive hydrogen sulphide medium for a single loadcase was added.
- The capability to set the dead loads for automatic calculation of stress ranges was added.
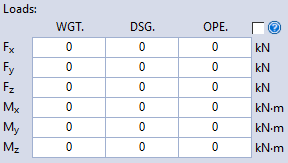
- The flexibility and SIF calculations were refined; the calculation is performed now at the ambient temperature, by default.
- The capability to generate result tables (allowable loads, flexibilities and SIF) selected from extreme values and received for different temperatures was added.
- The capability to set strength factors and fatigue strength reduction factor for any weld seam was added.
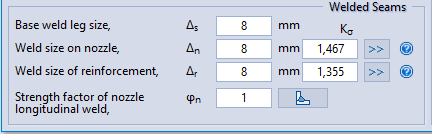
- The spherical unbeaded head (cover) model was added.
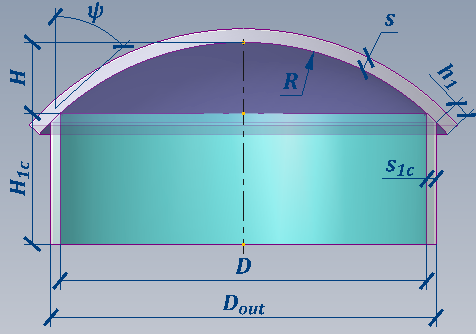
- The additional postprocessor options were added (rotation around object centre, rotation in cylindrical CS and etc.).
- The capability to display the applied loads in the postprocessor was added.
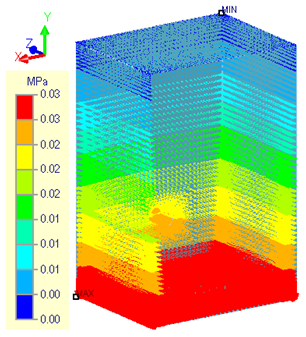
- The adjustment of postprocessor colors and shown elements was extended.
- The capability to open and save program data to XML file was added.
- The import of PASS/EQUIP XML files was added.
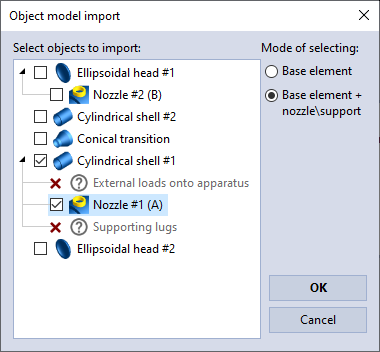
- The capability to insert a bend (elbow) nozzle by offset from second end (as for bend stanchion) was added.
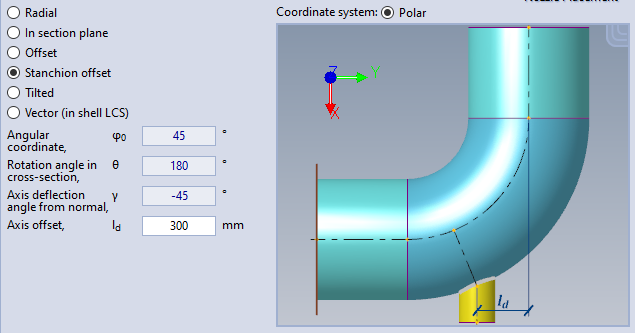
- The capability for models of conical reducer and head to set zero length for cylindrical and reinforcement parts was added.
- The algorithm of HTML report generating was refined (in particular, now the report folder contains only those pictures that are used in it).
- The capability to select the HTML report figure type for default generating was added (generic view or nozzle junction, together or separately, etc.).
- The capability to save HTML report figure type by control buttons with the subsequent transition to RTF report was added.
- The capability to output the number in a scientific format in an HTML report was added (for example, 1.0E+03).
- The dialog window of the RTF report generation was refined.
- The dialog windows of the generic and postprocessor settings, calculation progress were refined.
- The import of application system settings from previous versions was added.
- The error in the program's operation with the file system on Asian versions of Windows was fixed.
- The error of area merging for large models was fixed.
- The assessment algorithm under test conditions for JB 4732-1995 was corrected.
- The design diameter definition of holes for convex heads was changed as per the formulation of GOST 34233.3.
- The User Manual was refined.
|
3.3.1 06.06.2021 |
- The interface error when the radiobutton states were not saved in the project file was fixed.
- The report generator error, when the few sections were not formed for a certain load combinations, was fixed.
- The SIF calculation for elbow (bend) and head pipe (tee) with long legs was fixed.
|
3.3.2 07.07.2021 |
- The capability was added in the settings to select the initial or deformed model states for output in the report by default.
- The control button was added in HTML report to select picture with the initial or deformed model states.
- The error of the nozzle length checking when the calculating "In junction" was fixed.
- The import of weld factors from PASS/EQUIP XML file was fixed.
- The excessive CPU usage in the background was fixed.
- The error of transition from polar coordinate system to Cartesian coordinate system in the parameters of nozzle insertion was fixed.
- The error of displaying user interface 3d images when the screen resolution is set to over 100% was fixed.
- The error of load component indexing in the report tables of the initial data was fixed.
- The error in calculating of allowable loads, SIF and stiffness was fixed, which led to the fact that the design\operating conditions were not inherited.
The error appeared when loads were not specified.
|
3.3.3 21.07.2021 |
- The calculation error for projects opened from archive files was fixed.
- The error of displaying messages from materials database dialog boxes was fixed.
|
3.3.4 27.07.2021 |
- The reversing of skirt support model along the vertical axis was fixed.
- The calculation error of skirt support model without transition segment and nozzle was fixed.
- The alignment of user material database dialog box was fixed.
|
3.3.5 31.08.2021 |
- The use of tabular allowable stresses from JB codes was added when model is calculated as per ASME and GOST codes.
- The error of material database dialog box launch on Chinese language was fixed.
- The error of missing some templates for JB codes was fixed.
- The import error of model with adjacent element to nozzle from PASS/EQUIP XML was fixed.
- The output error of Mx1, Mx2, My1 and My2 in force units when calculating according to GOST 34233.3-2017 was fixed.
|
3.3.7 08.10.2021 |
- The restriction on the limit number of cycles in the input data verification was removed.
- The fatigue strength assessment by the Smooth Bar Fatigue Curve was corrected (ASME BPVC.VIII.2).
- The output of fatigue damage factor in the report was added.
- The error of the calculation running as per WRC 537/107/297 or GOST 34233.2,3-2017 was fixed.
- The error in accounting for hydrostatic pressure when was fixed when calculating as per WRC 537/107/297 or GOST 34233.2,3-2017.
- The error of the generation running RTF-report was fixed.
|
3.3.8 28.10.2021 |
- The error of report generating for a model without attachment was fixed.
- The table 5B (ASME BPVC.II.D) of program data base of titanium alloys was fixed.
- The definition of allowable stresses as per ASME BPVC.VIII.2 (classes 1, 2) was clarified.
- The definition of allowable stresses as per GOST 34223.1 for materials from ASME BPVC.II.D was clarified.
|
Version |
Update list in 3.2 |
3.2 09.05.2020 |
- The model of the bend (elbow) was added.
- The model of the bend stanchion (bend with trunnion) was added.
- The allowable loads, stiffness\flexibility factors and SIF were added for bend leg and support junction.
- The model of the support conical skirt was added.
- The model of the support skirt with an opening was added.
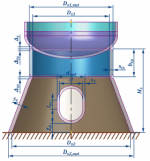
- The additional sections to runhead pipe was added which may have a different thickness.
The program reduces restrictions for nozzle inserting for this case.
- The non-circle nozzle shapes were added.
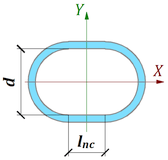
- The load application in WRC 107/297 designations was added.
- The capability of conical shell creating by angle of wall slope was added.
- The capability of single temperature setting for cylindrical part of heads was added.
- The capability was added to set own temperature for an attachment without adding thermal strains
to take only elasticity properties and allowable stress.
- The junction calculation from external loads by GOST 34233.3-2017 was added.
- The calculation of cylindrical part of head by GOST 34233.2-2017 was added.
- The setting of operation and test conditions was transferred in loadcase data.
A loadcase may have own work\test condition now.
- The capability was added to disable hardware acceleration of 3d graphics
to eliminate operation defects for unsupported graphical adapters.
- The generation of FE-beam model for conical reducer with cylindrical parts was fixed.
- The calculation of external diameter for flat head was fixed.
- The error of creating of hemispherical head FE-model without nozzle was fixed.
- The UI-columns of shell and nozzle loads was rearranged.
- The plots of material properties was added.
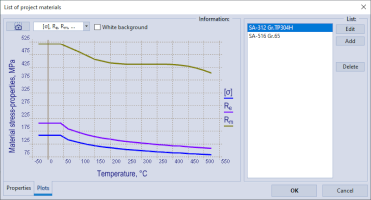
- The program manual was significantly redesigned regarding the description of elements, etc.
|
3.2.0.1 05.06.2020 |
- The error of the stress calculating from thermal strains for the cylindrical part of heads has been fixed.
|
3.2.0.2 17.06.2020 |
- The error of elements alignment procedure is fixed, that could lead to calculation aborting.
- The error of junctures calculating of conical reducers and heads according to GOST 34233.3-2017 is fixed.
- The calculations of cylindrical parts of conical reducers and heads according to GOST 34233.3-2017 are added.
|
3.2.0.3 25.06.2020 |
- The error of merging bottom area with convex areas for heads without cylindrical parts is fixed.
|
3.2.0.4 01.10.2020 |
- The error of report images creating with empty dimensions was fixed for some types of graphical adapters.
- The error of model with nozzle beading building was fixed when: dout > D, dmid < Dmid.
- The error of the report table of flexibility factors generating was fixed.
|
3.2.0.5 20.10.2020 |
- The opening/closing error the postprocessor window was fixed.
- The converting nozzle loads error was fixed when nzl-file importing created in the PASS/EQUIP Vessel.
- The conversion error of values specified in a unit system other than SI was fixed when nzl-file importing.
- The designations in report tables were fixed when using loads specified in the WRC coordinate system.
- The creating error of a model of an equal-pass tee was fixed with zero internal part.
|
3.2.0.6 04.02.2021 |
- The error of modeling tank with low type reinforcement was fixed.
- The error of modeling tank lowest seam is fixed.
- The error of hydrostatic pressure applying to branch of support skirt was fixed.
- The error of modeling flat oval nozzle with zero plane part was fixed (branch of support skirt).
- The calculation of general membrane stresses for nozzle reinforcement area was fixed.
- The allowable stresses calculation for general membrane stresses was fixed (mesh level factor is no longer taken into account).
- The allowable stress calculation as per JB 4732-1995 was fixed, when Rm,t was used instead Rm,20.
- The bend stanchion inserting by ld was fixed (that was corrected according to UI figure: negative values is right, positive values is left).
- The nozzle inserting by direction (nx,ny,nz) in bend (elbow) element was fixed.
|
Version |
Update list in 3.1 |
3.1 20.01.2020 |
- The model of torispherical head was added.
- The models of conical reducer and head with a knuckle\flare were added.
- The model of support skirt was added.
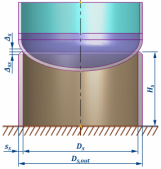
- The calculations in testing and mounting condtions were added for all codes/rules.
- The capability of axial direction (axis Z) of head and rectangle plate inverting was added.
- The dialog boxes were added that simplify the weld factors setting as per GOST 34233.6-2017.
- The reduced membrane stresses are now calculated with the shear stress for WRC 107(537)/297.
- The stress test as per equation (13) GOST 34233.1-2017 was fixed,
when allowable stresses are set by limits of the creep and the long strength.
- The procedure of auto selecting of model view was fixed for the generation of report images.
- The program error was fixed when working with material properties that are set at negative temperatures.
- The setting of shell and nozzle loads was transferred in the single tab and the corresponding united dialog box.
|
3.1.0.1 05.03.2020 |
- The calculation of conical shell with knuckles as per GOST 34233.2-2017 was added.
- The setting of concentrated loads on the shell element was fixed (runhead pipe, conical reducer).
- The figures in part of the weld seam notations were fixed for help and reports with results.
- The creating of the nozzle model with beading and welded segment was fixed.
- The creating of the conical head with knuckles and a nozzle was fixed (the nozzle placement wasn't correctly defined).
- The safety work was fixed for the some modes of interconnection with the local dongle.
|
Version |
Update list in 3.0 |
3.0 08.10.2019 |
- The new graphical user interface released.
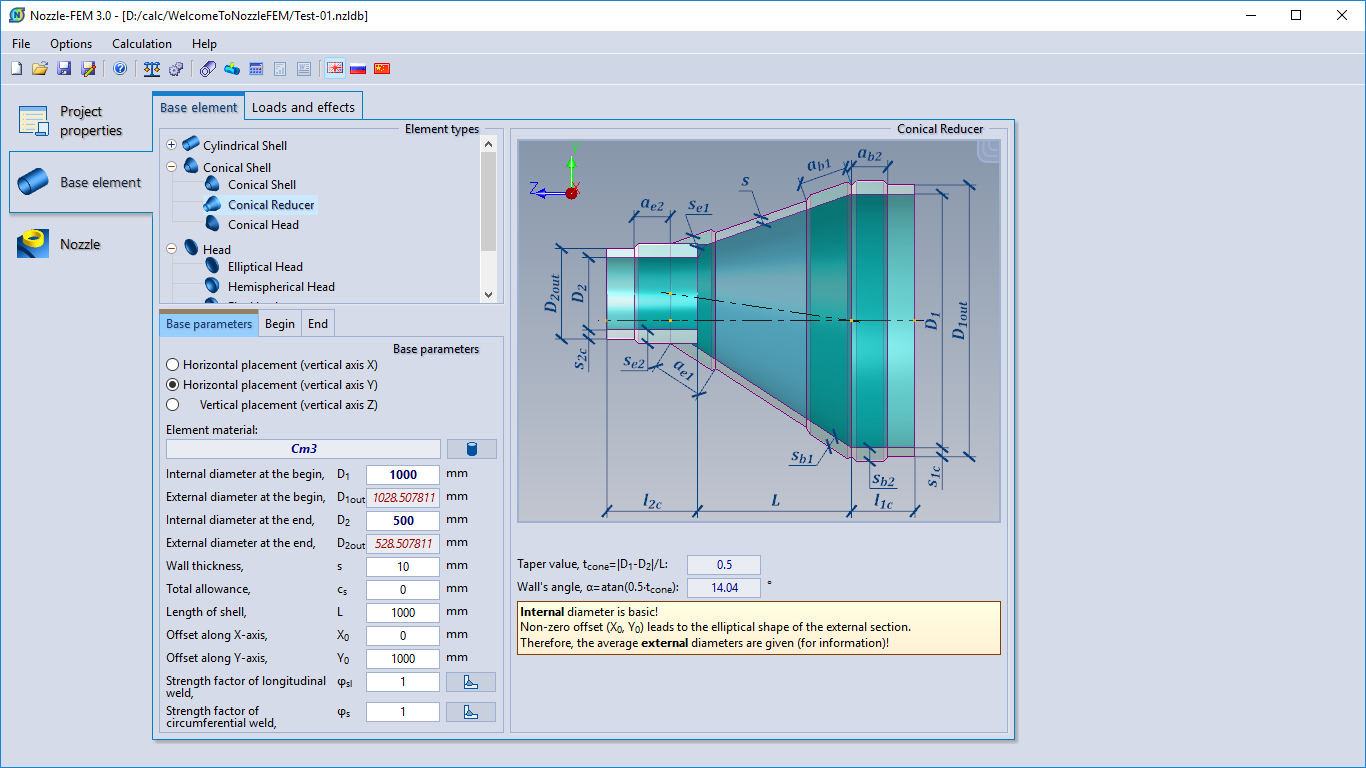
- The capability to change the orientation of all shell types was appended.
- The capability to insert a nozzle on the conical reducers and heads was appended.
- The capability to calculate a shell without nozzle was appended.
- The vector type of nozzle placement setting was appended.
- The capability to set some load cases in single project was appended.
- The new system coordinates (pipe CS) was append to set shell and nozzle concentrated loads.
- The calculations as per WRC 537 was updated.
- The calculations as per GOST 34233.2,3-2017 was fixed.
|
3.0.0.1 21.10.2019 |
- The barrel appending error has been fixed.
- The report export to RTF format has been fixed, in participle, the generation of tables with merged cells is updated.
- The error of measure unit "kgf·cm" using has been fixed.
- The error of MS Word program running for RTF-report editing has been fixed.
- The output of the allowable loads of table 2 when set hydrostatic pressure has been fixed.
- The precalculation verification of physical and mechanical material properties has been fixed.
- The error of a project saving with unused materials has been fixed.
|
3.0.0.2 1.11.2019 |
- The calculations of allowable loads, stiffness and stress intensification factors were appended
for shells in the models of tee and conical reducers.
- The discrepancies of export to RTF-file were fixed.
- The report discrepancies of coordinate system figures with the calculated results were fixed.
|
3.0.0.3 13.11.2019 |
- The export to RTF-file for OS Windows 7 has been fixed.
- The error of the tee creation with equal run and branch parts has been fixed.
|
Version |
Update list in 2.16 |
2.16.0.2 11.02.2019 |
- The error has been fixed that occurred in some cases when the corrosive hydrogen sulphide medium was enabled.
- The errors of program GUI have been fixed, in particular:
when for the nozzle with beading it was necessary to set the weld seam parameters;
if the TANK flag for a cylindrical shell was before enabled then the model of tee (main pipe) was not correctly created.
- The error of central nozzle insertion on the elliptical head has been fixed,
that occurs sometimes in exceptions of floating point operations.
- The error of distribution package has been fixed where the installation language ID was not recorded,
after which the program could not load resources correctly.
- The report generation error has been fixed that occurred in the absence of all loads and that led to the program termination.
|
2.16.0.1 16.01.2019 |
- The error of stiffness calculation with the exclusion of beam stiffness has been fixed.
This error could lead to mistakes of stiffness (from 10 to 25 percent)
when the checkbox "Exclude the beam model" is enabled.
This error had no influence on other calculation types.
- The restriction of hydrostatic pressure setting for the heads has been removed.
Now can set the hydrostatic pressure for all models, but only along the vertical axis.
- The misprints in the report templates have been fixed (in particular, calculation by WRC 107(297), the misprint GOST 34233.X-2007).
|
2.16.0.0 28.12.2018 |
- New: calculation of thermal strains has been added,
which allowed to analyze additional stresses arising from constrained temperature strains or
action of different temperatures in the components.
For more information, see
"Thermal strains".
- New shell type has been added - rectangle plate:
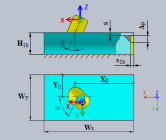
- New: strength verification tests has been updated and revised for ASME BPVC.VIII.1-2017.
- New: strength verification tests has been updated and revised for ASME BPVC.VIII.2-2017.
- New: strength verification tests has been updated and revised for EN 13445-3:2014 (E) Issue 4 (2017-07).
- Strength verification tests has been updated and revised for GOST 342233.1-2017.
In particular, a verification test has been added for materials that work at temperatures in the range where creep and stress rupture govern the selection of stresses.
- Strength verification tests has been revised for GOST 342233.6-2017.
- Strength verification tests has been revised for GOST 342233.10-2017.
- Calculation method for "On the edge" and "In junction" has been significantly changed.
For more information, see
"Calculated nozzle length".
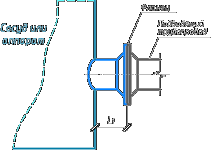
- Calculation of elliptical heads with ratio $H/D \le 0.25$ has been allowed.
- The fillet radius for nozzle with beading sets now the radius of the middle surface (that is, it is no longer recalculated).
Verification of radius is now performed by condition: $r \ge 0.5\min\left\{s,s_1\right\}$.
- The bug of insertion of vertical nozzle has been fixed on the hemispherical head.
|
Version |
Update list in 2.15 |
2.15.0.6 01.11.2018 |
- The materials properties was clarified for EN 10216-5 and EN 10217-7.
- The geometrical and finite element models of nozzle junctions was clarified.
- The error of conical shells parameterization with a large cone angle (large taper) is fixed.
|
2.15.0.5 15.10.2018 |
- The parameter check of weld-in toroidal insertion for tilted nozzle is improved.
- The error of tank model creation with low type reinforcement is fixed.
- The error of flat head model creation with the central radial nozzle is fixed.
- The allowable load tables titles for calculations with low-cyclic loads is renamed by allowable load amplitudes.
|
2.15.0.4 24.09.2018 |
- The error of stiffness matrix invalid factorization at large mesh levels is fixed (error # 803 in versions 2.14 and below).
- The bugs of conical shell modeling with large offsets is fixed.
- The bugs in GUI for the calculated schemes of the conical bottom and the reducer is fixed.
- The misprints in the GUI when choosing the strength calculation under low-cycle loads is fixed.
- The bug of geometrical model creation of tilted nozzle with short length is fixed.
- The bug of average radius calculation on flat heads is fixed.
- The bug in the GUI is fixed when the digits after the comma were lost (for a some Windows regional settings).
- The minimum allowable distance from the outer surface to the shell edge was reduced (condition was lighted).
Now, instead of $d/2$, we use criterion $\min\left\{d/2,\sqrt{Ds}\right\}$.
- The incorrect output of allowable stress values for austenitic steels is fixed (in the calculations the correct values is used).
- The bug of mesh alignment in the extrapolation stress procedure is fixed when the nozzle welded zone ≤ 2·s1.
- The inaccuracy of result nozzle thickness calculation with inner part is fixed (in strength calculation addition cs1 was only applied).
|
2.15.0.3 28.08.2018 |
- The visualization of the window zoom mode in the postprocessor is corrected.
- The generation of the finite element framework in the postprocessor when changing display modes is corrected.
- The formatting of reports for calculations under GOST 34233.2-2017 and GOST 34233.3-2017 is corrected.
- The error of reports generation on non-European versions of Windows 10 when choosing Russian language is fixed.
- The blocking of the solution stage during the nozzle length testing is fixed.
- The verification of material properties at a given operating temperature is supplemented.
|
2.15.0.2 20.08.2018 |
- The error of running the solver when working with files located in a network folder is fixed.
- The error of dongle access customizing is fixed.
- The error of postprocessor running for some cases of regional floating point number representation is fixed.
- The error of calculation running for newly created projects is fixed.
- The system of requests to the user when saving and calculation running is modified.
- Bugs of handling related GUI elements is fixed.
- The presentation of calculation results is fixed.
- The error of creating edge elements on the nozzle short inner part is fixed.
- The inaccuracy in the geometric model construction of elliptical heads on the areas of sharp curvature changes is fixed.
- The inaccuracy in the geometric model construction of the conical transition and bottom with the left cylindrical insertion is fixed.
- The inaccuracy in the parametric model of the conical shell with a "small" height is fixed.
|
2.15.0.1 08.08.2018 |
- The limiting temperature is introduced when corrosive medium is actived in accordance with GOST 34233.10-2017.
- The calculation of allowable stresses for nozzle with pad was modified.
- The critical error in the design model of conical reducer and head is fixed.
- Flaws related to the materials database is fixed.
- Flaws in the installation program associated with the installation of Microsoft Visual C++ 2015 Redistributable is fixed.
- Edge artifacts on short fittings is fixed.
- Flaws in creating a geometric model of an tee with equal run and branch parts is fixed.
- The critical error in the stress extrapolation procedure on short fittings was fixed which caused the solution abort.
- The text formatting in reports is corrected.
- The incorrect output of allowable stresses for JB 4732-1995-EN is fixed.
|
2.15.0.0 27.07.2018 |
- Version 2.15 is installed only on 64-bit versions of Windows.
- The finite-element solver was translated on a 64-bit architecture and
this is allowed to escape from memory restrictions (1.5Gb) for 32-bit Windows versions.
- The calculation method of allowable loads was corrected and refined.
- The calculation method of stiffnesses and flexibily factors was corrected and refined.
- The calculation method of stress intensification factors (SIF) was corrected and refined.
- The procedure of stress extrapolation at the weld toe was added,
which allows to more accurately estimate peak stresses, improve the convergence of stress values at different mesh quality levels.

- For conical shell was added the possibility of specifying the end offset (as for eccentrical reducers):
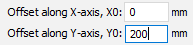
- Load of hydrostatic pressure load was add for cylindrical and conical shell:
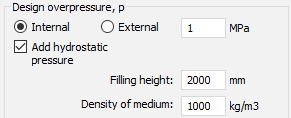
- Nozzle type radiobuttons was replaced by nozzle type combobox:
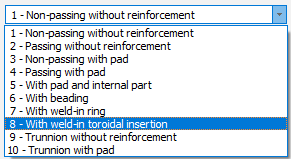
- The new nozzle type "with weld-in toroidal insertion" was added:
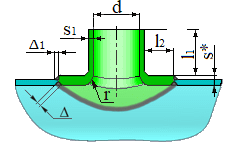
- The new nozzle type with beading was added:
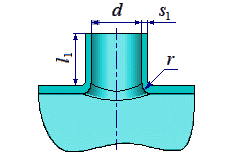
- The new nozzle type with beading and with welded segment was added:
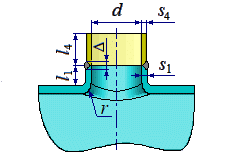
- The regeneration possibility of the result report was added.
- The result report was changed for allowable loads, stiffnesses and stress intensification factors sections.
- The postprocessor possibilities was extended for color setting of background, element edges and etc:
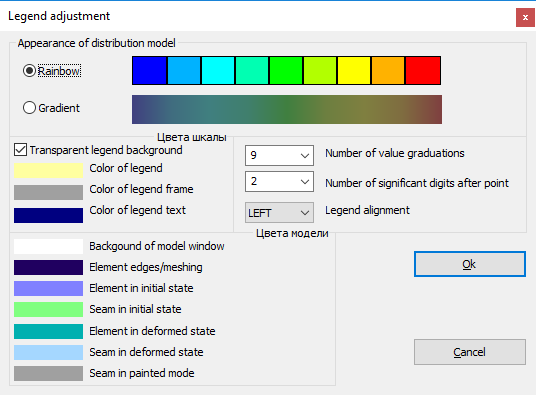
|
Version |
Update list in 2.14 |
2.14.0.7 02.04.2018 |
- Fixed error that occurs when using materials of EN 13445-3 when calculating to EN 13445-3.
- Fixed some typos in the GUI.
|
2.14.0.5 29.12.2017 |
- Restrictions was removed on the use of alloys from non-ferrous metals.
- The database of materials was extended.
|
2.14.0.4 27.11.2017 |
- The calculating method of material characteristics was refined.
- The output of allowable stresses in the source data for some ASME-materials was fixed.
|
2.14.0.3 10.05.2017 |
- Fixed the error for inserting a nozzle into elliptical bottoms for a private subtask.
|
2.14.0.2 10.05.2017 |
- The algorithm for generating a finite element grid on elliptical bottoms is optimized.
- Fixed errors translating into Chinese language.
|
2.14.0.0 17.03.2017 |
- Postprocessor module (3D interactive model) was developed. It helps to visualize the results of calculation.
- Materials database was filled by mechanical properties of materials from GB 150.2-2011 (China).
|
Version |
Update list in 2.13 |
2.13.0.0 06.12.2016 |
- Added strength calculation under low-cyclic loads as per i.7 GOST R 52857.6-2007 "Improved calculation to low-cycle strength".
- Corrected safety factor for austenitic chrome-nickel steels as per GOST R 52857.1-2007.
- Strength calculation of V-th vessel group working in corrosive hydrogen sulphide environment (GOST R 52857.10-2007).
- Fixed flat head description in report.
|
Version |
Update list in 2.12 |
2.12.0.1 05.07.2016 |
- Weld seam mesh was refined and elements along nozzle were overridden.
- Materials database working faster.
- "Delta" was removed for nontransition nozzles with pads.
- Wall's angle calculation for conical shell added to program interface.
- Tilted nozzle's location was corrected.
- User template report's path is saved on exit.
|
2.12.0.0 14.03.2016 |
- Nozzle location limit for bottoms/heads are expanded.
- Calculation of conical transitions and heads clarified due to refined mesh.
- Chinese language is allowable for working.
- Added calculation of the stress intensification factors.
- Added calculation of the flexibility factors.
|
Version |
Update list in 2.11 |
2.11.0.1 28.05.2015 |
- Fixed encoding bug in the Html report.
|
2.11.0.0 22.05.2015 |
- Stiffness calculation in junction for all model configurations.
- Strength estimation as per ASME VIII div.1.
- Strength analysis of conical transition and heads working in corrosive hydrogen sulphide environment (GOST R 52857.10-2007).
- Added criterion for ASME VIII div.1,2: "Protection against local failure" (σ1+σ2+σ3≤4[σ]).
- Materials database was filled by mechanical properties of materials from tables 1A, 1B (ASME II Part D (Metric)).
|
Version |
Update list in 2.10 |
2.10.0.0 25.09.2014 |
- Strength analysis of conical transition and heads.
- Strength estimation as per JB 4732-1995.
- Materials database was added by mechanical properties of materials from JB 4732-1995, GB 713-2008 and TU 14-3P-55-2001 Standards.
|
Version |
Update list in 2.9 |
2.9.0.0 02.12.2013 |
- Strength estimation as per ASME VIII Div. 2 2010 and EN 13445-3:2002 E.
- Analysis of barrel nozzles.
- Stiffness estimation in junction place, as well as on the edge of nozzle.
- Materials database was added by mechanical properties of main materials from EN Standards.
- Materials database was added by "Maximum allowable stresses" (table 5(A, B)) from ASME Sect. II, Part D for estimation by Sect.VIII, Div.2.
|
Version |
Update list in 2.8 |
2.8.0.4 14.06.2013 |
- Fixed bug of saving update settings;
- Materials database was added by mechanical properties from PNAE G-7-002-86, OST 26-01-858-94, STO 00220227-006-2010, GOST R 54522-2011.
|
2.8.0.0 26.07.2012 |
- New FE-model for estimation of strength and stiffness of nozzles connections into the vertical steel tank's walls, including nozzles with tombstone shape reinforcing plate.
- Analysis of trunnion connections.
- Implementation of a new material database, which includes both Russian and ASME material properties.
- Automatic software version update system is introduced.
|
Version |
Update list in 2.7 |
2.7.0.0 09.08.2011 |
- Added converter for making RTF reports, using one of default templates.
- Head's straight flange mesh became a fine structure.
|
Version |
Update list in 2.6 |
2.6.0.0 14.10.2010 |
- Straight flange and cylindrical shell was added to head model.
|
Version |
Update list in 2.5 |
2.5.0.0 01.02.2010 |
- Added standards for strength estimation: GOST R 52857.1-2007 and GOST R 52857.10-2007 (corrosive hydrogen sulphide environment).
- Reduced minimal limit distance from nozzle's wall to shell's edge.
- Number and longitudinal length of shell's elements are optimized.
- Loads to tilted branch can be applying as in the main pipe coordinate system and in the branch;.
- Added the ability to configure the number of stress contours (from 3 to 30).
|
Version |
Update list in 2.4 |
2.4.0.0 21.07.2009 |
- Program was expanded by english language interface with switching on fly.
- Added models of radial and tilted branch connections. Loads applying points are on the main pipe and on the branch.
- Tables are free from pictures, what is good usable for MS Office.
- Reduced minimal limit distance from nozzle's wall to shell's edge.
- Deformed model picture in auto scale added to the report.
|
Version |
Update list in 2.3 |
2.3.0.0 20.01.2009 |
- Added nozzle calculation, including allowable loads and stiffnesses, for both global and local coordinate system.
- Realized calculations of junctions of both horizontal and vertical shells.
|
Version |
Update list in 2.2 |
2.2.0.0 13.11.2007 |
- Improved user interface and fixed bug with wrong nozzle location in the conical shell.
|
Version |
Update list in 2.1 |
2.1.0.1 27.06.2007 |
- Fixed some minor bugs in dongle working.
|
2.1.0.0 29.11.2006 |
- The first commercial version of the program, which replaced program "Nozzle".
|